半導体製造業界への適用事例
半導体製造には、半導体材料の切り出しからウエハ上の電子回路の形成、ICチップのパッケージなど多段階の工程があります。
半導体デバイスは非常に小さなサイズで作られており、外観検査自動化のためには高解像度のセンサーが必要です。また一度に大量のチップが生産されるため、その生産速度に追いつくような高速なインライン検査が求められます。
3Dセンサーは半導体製造工程の様々なシーンで精密なインライン検査を行うために活躍しています。
事例1 シリコンウエハの外観検査
インゴットから切り出したウエハはCMP装置で平らに研磨されます。時間の経過とともに摩耗する研磨パッドの表面は定期的に検査する必要があります。
共焦点3DセンサーGocator5500でウエハの表面を3Dスキャンし、高さデータから摩耗につながる微細な凹凸変化を検出します。
また、ウエハから個々のダイを切り出すダイシング工程においても3Dセンサーが活躍します。
ダイシング技術の一種であるスクライブではレーザーやダイヤモンドブレードでチップを個々に切り出すためのスクライブライン(溝加工)を施します。
ブレークする前にスクライブラインの溝位置や深さ、カーフ幅を3Dセンサーで高精度に計測することで、ダイチッピングなどの欠陥を低減します。
シリコンウエハのように光沢の強いガラスのような表面や、エッジ部の斜面も共焦点3DセンサーGocator5500なら高精度に計測が可能です。
ウエハ表面の外観検査
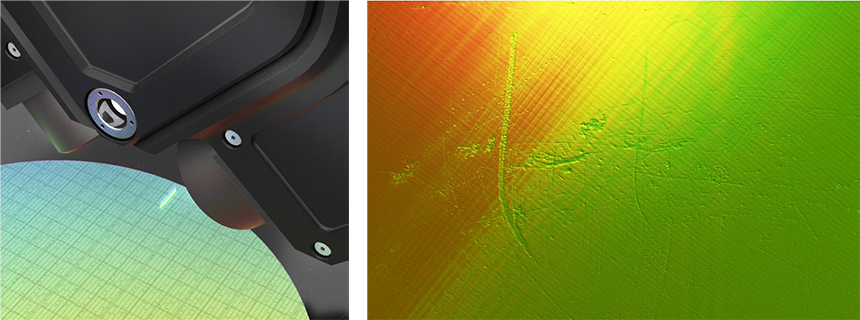
スクライブラインの溝深さ計測
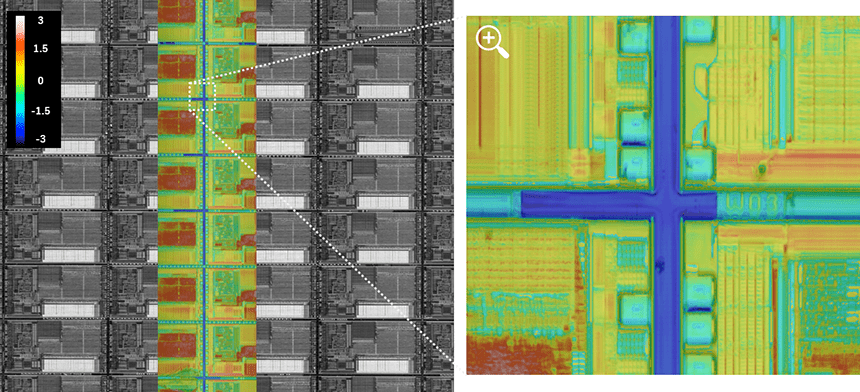
事例2 BGA/PGA検査
BGA(Ball Grid Array)チップは、SMT実装を用いて高密度な接続を可能とする代表的なICチップです。
チップ底面に高密度に配置された極めて小さい半田ボールやピンの高さ・位置・直径をサブミクロンの計測精度で正確に測定します。
リンクスで扱う3Dセンサー(Gocator5500、3DPIXA、heliInspect)はBGAのボールサイズや検査内容に応じて各BGA検査工程で活躍しています。
共焦点3DセンサーGocator5500は、直径50μm以下のボールの高さ・位置などの寸法情報を正確かつ高速に測定することができます。
超高精度3DエリアセンサーheliInspectでは真上からワンショットで高精度3DデータをスキャンすることでPGAの極小さいピン先端高さも高精度に計測可能です。
3Dラインスキャンカメラ3DPIXAでは複合照明を用いることでボール径や基板面の検査などBGA基板全体の検査を一度にカバーすることができます。
共焦点3DセンサーGocator5500でのBGA計測
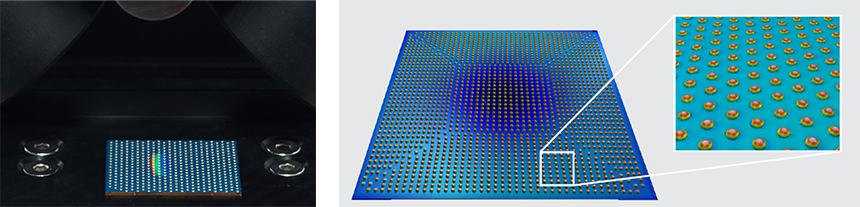
heliInspectでのPGA計測
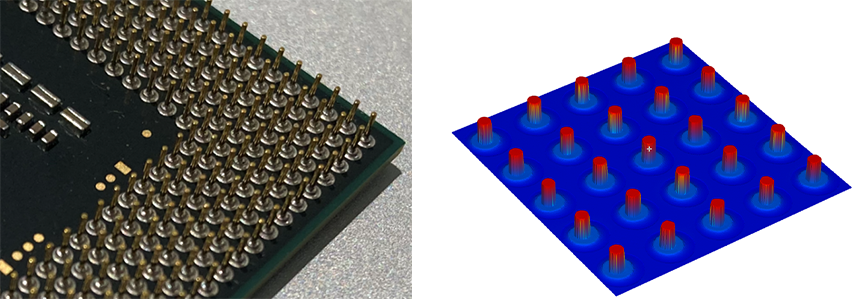
3DPIXA+複合照明でのBGA計測
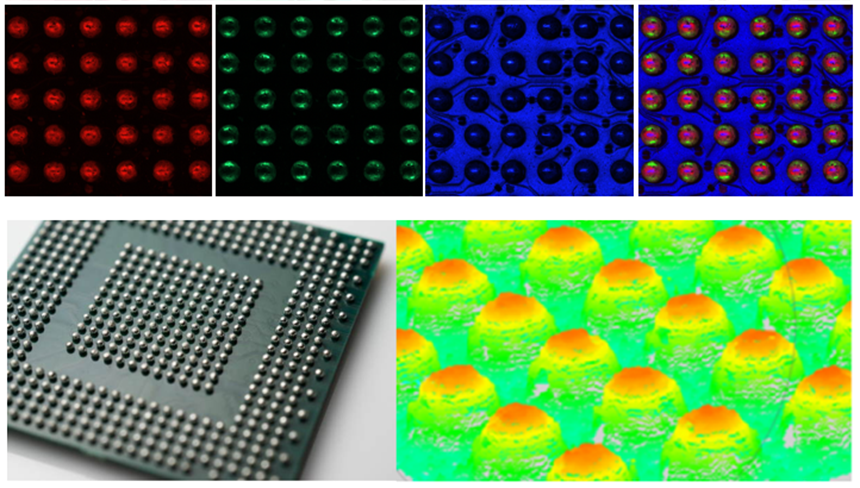
事例3 リードフレームの曲がり・コプラナリティ検査
半導体パッケージの主要部品であるリードフレームは、近年リードの細線化が進み、先端径が50µm以下のファインピッチリードも出てきています。
このような50µm以下の極細リードを安定して検査するためには10µm以下の分解能での撮像が必要です。
リードフレームのサイズは幅100mm程度のものも多く、解像度と視野を確保するため2Dの高解像度カメラで検査していました。しかし、2次元撮影ではリードの浮きや凹みまでは捉えることができません。
またX解像度10μm以下の3Dセンサーは視野幅が10mm程度と狭く、リードフレームの全面検査を行うにはセンサーを何台も配置するか検査に時間をかける必要がありました。
3Dラインセンサー 3DPIXAは15,000画素のラインセンサーを2台組み合わせたステレオ撮影で広視野を高速・高精度に3Dスキャンします。
3DPIXA Dual wave 7umなら視野幅100mmを7μmピッチで、速度124mm/secで3次元計測可能です。
リードフレームの幅だけでなく、μmレベルの凹凸不良まで正確に検査します。
リードフレームのコプラナリティ検査
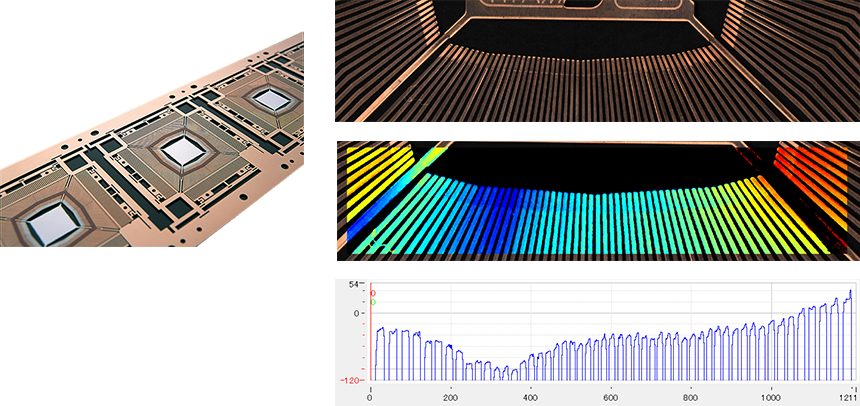
事例4 パッケージ基板の外観検査
半導体パッケージの実装に使用されるパッケージ基板の外観検査でもμmレベルの微小な凹凸欠陥の検出が求められます。
共焦点3DセンサーGocator5500では、基板上に見られる高さ1µmの微細な配線パターンも明確に捉えることができます。また高さ10µm程度の異物も捉えることができており、2D撮影では見逃してしまう微細な凹凸欠陥を検出します。
Gocator5512では視野幅12mmを最大フレームレート10kHzでスキャン可能です。
Gocator5512でのパッケージ基板計測
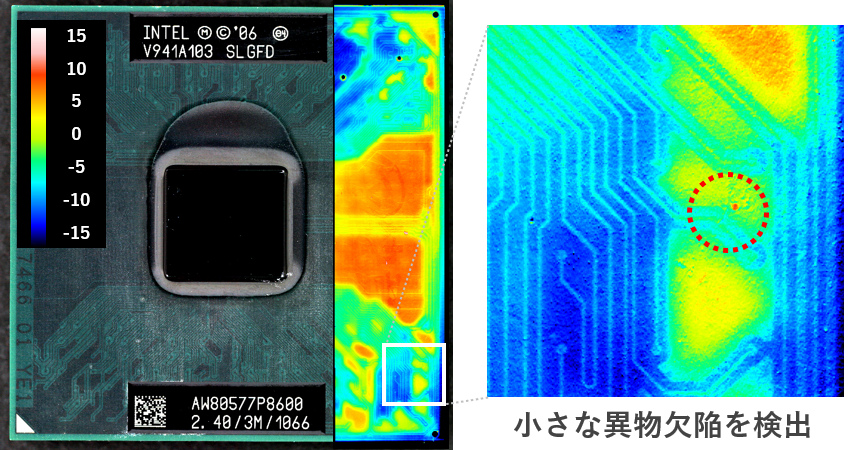
3Dラインスキャンカメラ3DPIXAはμmオーダーの高さ計測が可能です。1ラインあたり15,000ピクセルの高解像度センサーでパッケージ基板をワンスキャンで撮影します。
パッケージ基板検査は欠陥そのものが微小という課題もありますが、欠陥の種類が複数あり、全ての特性の欠陥を検出するところに難しさがあります。
基板の製造工程では最後に半透明のレジスト膜を塗布します。欠陥がこのレジスト面上の凹みとして表れることもあれば、レジスト塗布前の素の基板パターン回路に発生する場合もあります。2D検査では、これら特性の異なる欠陥に対して画像センサーや照明条件をそれぞれ検討しなくてはなりません。
3D画像とカラー画像が取得できる3Dラインスキャンカメラ3DPIXAと同メーカーの複合照明という特殊照明を組み合わせることで、特性の異なる複数種類の欠陥検出を一度に行うことが可能です。
複合照明は、ドーム照明、暗視野照明、同軸照明の3つの異なる照明を1つの連結したもので、それぞれの方式に対して異なる色のLEDを割り当てています。
この照明でパッケージ基板を撮像すると、RGBの3チャンネルでそれぞれ特性の異なる画像が撮影されます。
例えばドーム照明では鏡面にあたるチップ上の異物を、同軸照明ではレジスト面上の異物が可視化できます。暗視野照明では基板上のパターンが鮮明に捉えられています。
これら3チャンネルの2次元画像に加えて、3Dラインスキャンカメラ 3DIPIXAでは高さ画像を撮影することができ、レジスト面にある10µm以下の凹みを計測します。
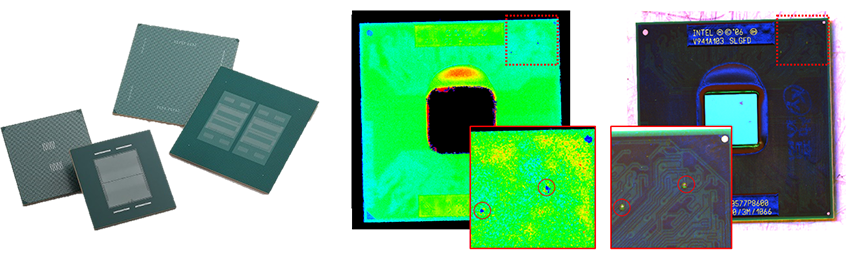
3DPIXA+複合照明でのパッケージ基板計測
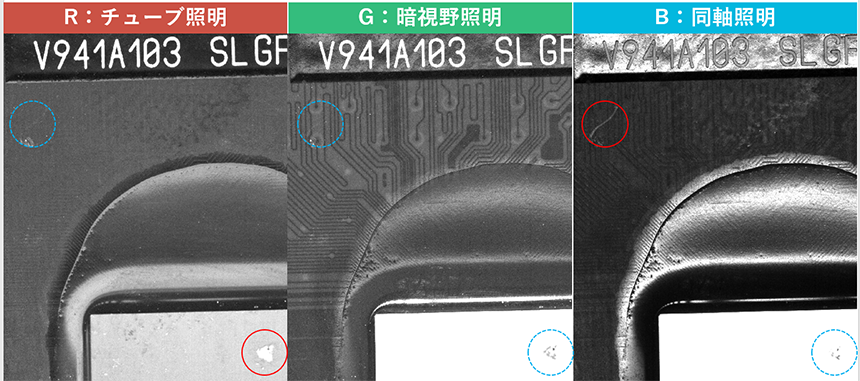
事例5 ワイヤーボンディング/ボールバンプの欠陥検査
ワイヤーボンディング工程では、チップとリードフレームの端子を太さ数十μmの金線で接続します。
ボンディングされたワイヤーに高さや位置のばらつきがないか、またワイヤーの切れや曲がりがないかなどの欠陥を検査します。
半導体製造に使用されるワイヤーは太さ20μm程で光沢もあり画像検査は難しいとされてきました。またワイヤーボンディングの検査ではミクロンレベルの検査精度が要求されます。
リンクスで扱う3Dセンサー(Gocator5500、3DPIXA、heliInspect)はいずれもミクロンレベルの計測精度を備えており、ワイヤーボンディング工程の検査で活躍しています。検査箇所・検査項目に応じて最適な計測手法を選択できます。
Gocator5500でのワイヤーボンディング計測
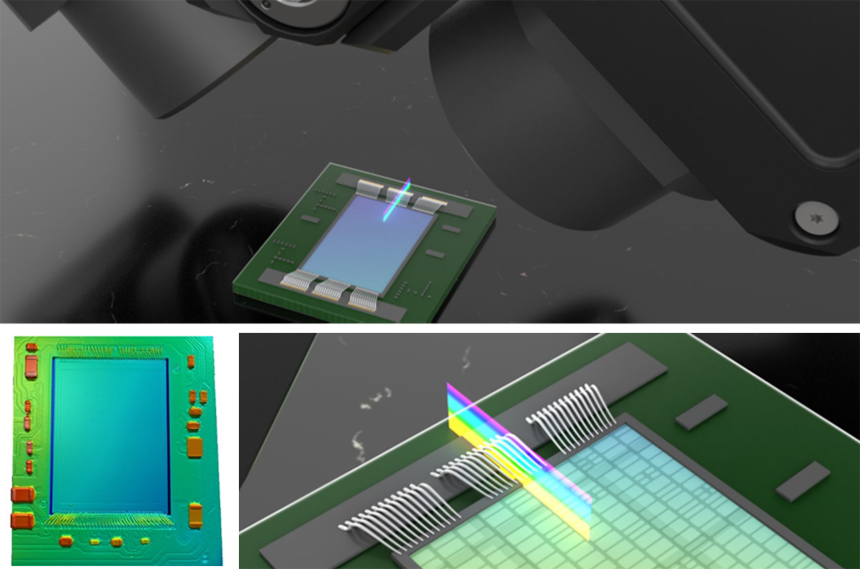
3DPIXAでのワイヤーボンディング計測
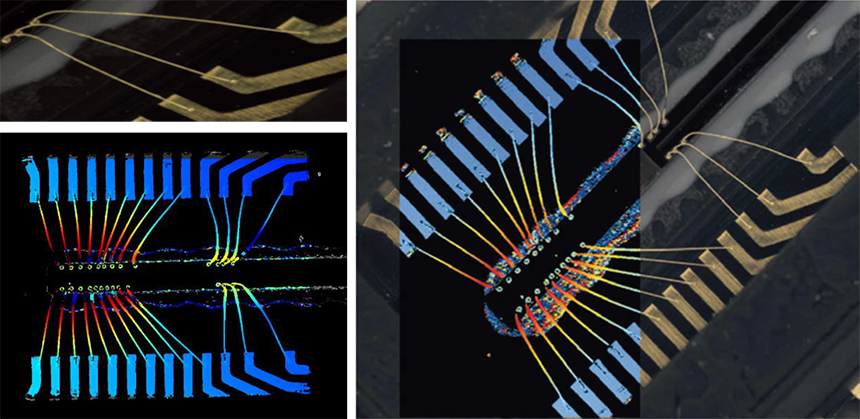